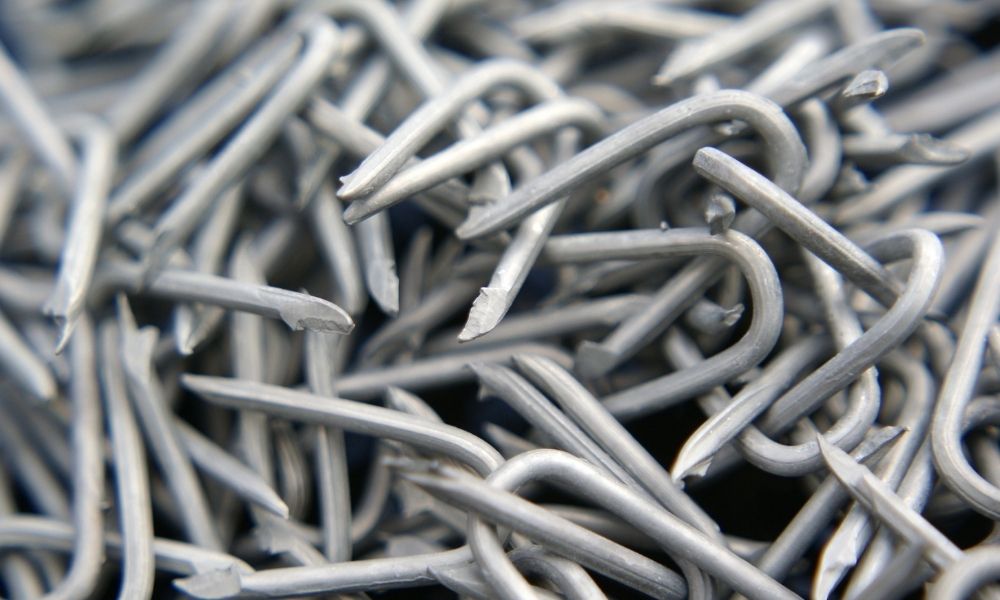
A staple’s a staple, right? Not so fast. Staples come in a wide range of types designed for various uses. They vary by size, including the width of the crown and the length of the leg. Some have flat crowns, while others intended to fasten cables to baseboards or along walls have curved crowns. But one thing all staples have in common is that they are made of wire.
Wire’s wire, right? Not exactly. The different staple wire types are adapted to specific uses and environments. They are made from different types of metal of varying thicknesses. Knowing the different staple wire types will help you know what kind of staple to load into your stapler for the job you need to do.
Understanding Different Types of Metal in Staple Wire
Staples can be unobtrusive or obvious, depending on the result you want. This is partly because of the type of wire that makes the staple. Exposure to humidity or harsh conditions like salt sea air or seawater can affect a staple’s longevity and ability to stay in place. Different types of metal used to make staples include:
Aluminum: this softer metal is good for staples that shouldn’t attract magnets. They are easy to remove and soft enough to cut without damaging a saw or scissors.
Galvanized steel: steel wire with a coating of zinc resists corrosion. Staples made of galvanized steel can handle humid or damp environments without corroding or rusting. As a result, they tend to last a long time.
Stainless steel: stainless steel staples have higher corrosion and rust resistance than galvanized steel, and they are more protected from heat and have more endurance for salty environments. They also look shiny and modern.
Copper-coated: most often used for closing cardboard cartons, copper-coated wire looks great and handle humid environments well.
Colored wire: standard office staples with a color coating for appearance or color-coding.
Monel: a nickel-copper alloy with smaller amounts of iron, manganese, carbon, and silicon, created in 1901 by Robert Crooks Stanley and named after the president of the International Nickel Company, this wire is even more corrosion-resistant than stainless steel and is very strong. Because of its properties and how it’s made, Monel is substantially more expensive than stainless steel.
Gauge
Staple wire thickness is measured by its “gauge.” This is a measurement of a wire’s diameter. The system of identifying wire by its diameter was originally developed 1857 to specify electrical wires by their current carrying capacity. Oddly, the higher the number, the thinner the wire. Wire is referred to as heavy, medium, or fine:
Heavy wire is typically 15-16 gauge, and used for the toughest jobs on heavy materials, like roofing or other construction materials. Heavy wire staples are also used for subflooring, framing, and for fixing boxes to pallets.
Medium wire measures 18-19 gauge and might be used for materials thicker than paper, but not as thick as wood or roofing used in construction. They’re good for heavy upholstery, paneling, cabinet construction, sheathing, and siding.
Fine wire measures 20-23 gauge. This is the type of wire you’ll see in a standard office stapler, but fine gauge wire also makes staples for trim, picture frames, furniture framing or assembly, and lighter upholstery. A pneumatic upholstery stapler may use 20 or 22 gauge staples, depending on the materials being fastened together.
When choosing staples, you must match the type of staple to the tool you are using to the job you’re doing. To do this, you should understand that staple types are defined not just by the type of wire they’re made of, but also by their width and the length of their “legs,” the parts that penetrate the materials you are fastening together.
Standard office staples are made of fine wire, 22 or 23 gauge, and their legs are ¼ inch long. Charts and packaging identifying staples will express this measurement as “23/6”, meaning the wire is 23 gauge, and the legs are 6 millimeters long. The more paper you must staple together, the longer the leg should be. But remember, you must match the staple to the tool. A standard office stapler will only accept a ¼ inch, or 6mm, leg. Heavy-duty staplers that can bind 200 pages or more may use a staple with a 20 or 24-millimeter leg.
To further complicate matters, staples with the standard “X/Y” (gauge, leg length) indication on the package may also have another number identifying their size, like “No. 10” or “No. 56.” Just be sure to read the entire description of the staple, and the stapler tool manufacturer’s recommendation about what size staple to use in your tool. Some manufacturers make staples exclusively for their own line of tools.
Whatever type of wire makes up a staple, every type of staple is bent into the desired shape (rounded or flat), width and leg length, either before it is loaded into the tool or by the tool applying it. Strips of staples are held together with glue, tape, or plastic. Some staples are coated with a type of glue that melts when a tool fires the staple, and then dries for an extra secure hold. A full strip is usually 200 staples, while a half strip is 100. Some staples come in coils or cartridges for industrial use, with thousands of staples per coil.
Staple wire is also worked to create the point or teeth at the end of the staple legs, usually chisel-shaped for best penetration of materials. Divergent staples have chisel points pointing outward in opposite directions, causing them to splay outward when applied for a better hold. They can be a bit unpredictable, so keep your hands and fingers well away from the area being fastened.
When selecting a staple, start with the type of work you’re doing and the tools you’ll use, as well as the materials you are fastening together. Make note of any special conditions, such as outdoor exposure to humidity or salt, considerations about the appearance of the result, and the quantity of staples you’ll need to complete the job. If you have questions about which staples match your tool or your project, contact Staple Headquarters for information.
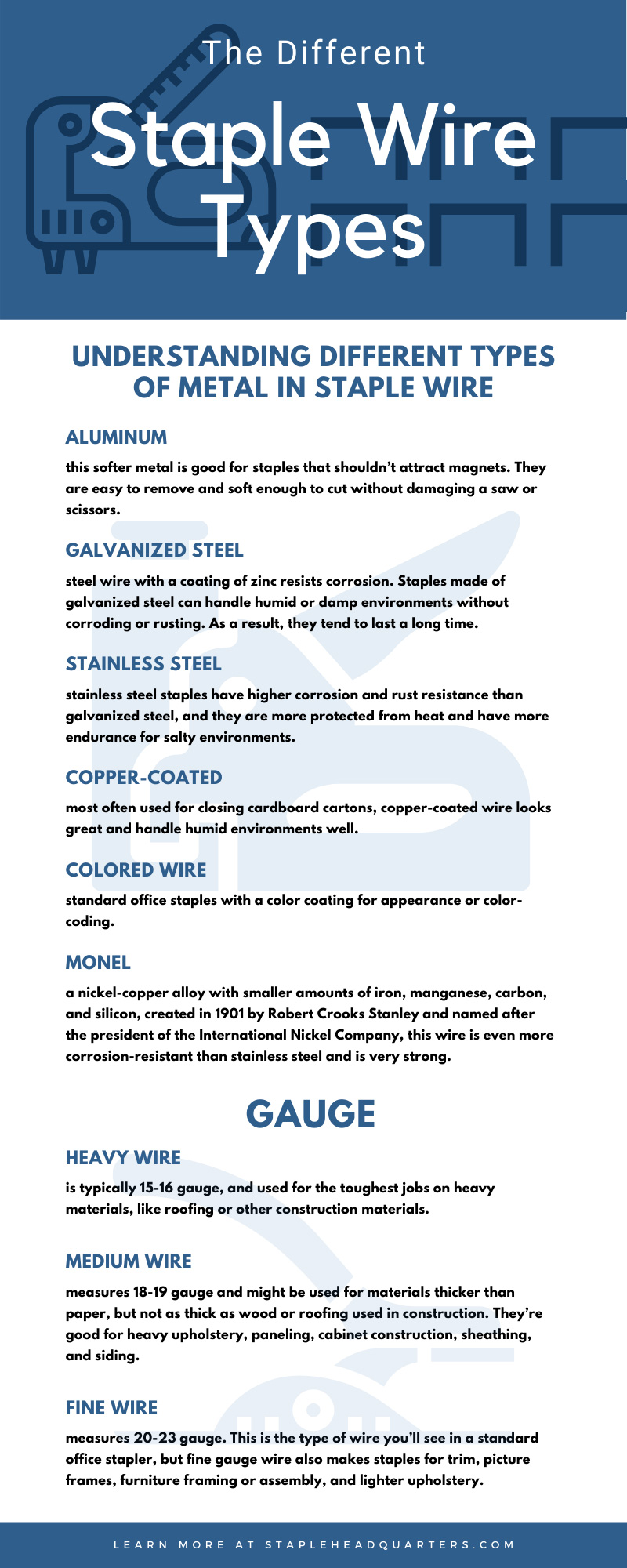